Design of High Strength Concrete Mix
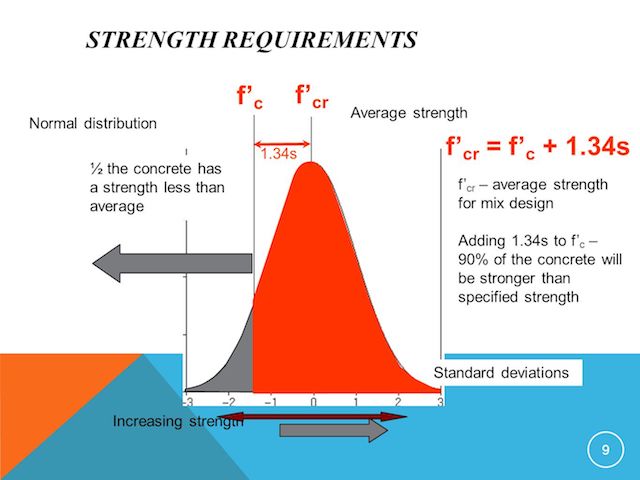
The type of concrete generally with compressive strength of 6000psi (40MPa) or greater is called as HSC
- We need high strength concrete in our modern infrastructures in order to put the concrete into service at much earlier stage, To build up high rise building by reducing column sizes and increasing available space or in case of long span bridges
Now what is mix design? Although the American Concrete Institute (ACI) doesn't use the term, preferring mix proportioning. But keeping in view the modern knowledge of concrete (especially in case of high strength concrete), we should improve the term proportioning to designing. It is everything that makes the concrete work well for application.
Proportioning Concrete
Part of mix design is to develop mix ratios that lead to high compression stresses at failure. The two criteria for a successful mix ratio are:
- High compressive stress
- Adequate workability
Once a mix ratio is selected, we need to compute the Amounts of cement, water, and aggregates required. The amount of these ingredients and the processing depend on weather the concrete prepare in laboratory or in field. Beside Proportioning HSC designing require study of the following aspects.
Selecting Maximum Aggregate Size
Remember that while discussing mix-design of High strength concrete the term "cement" is use to describe all the cementious materials in the concrete and not just the Portland cement. In general, smaller size aggregates have been shown to produce higher strength concretes, for a fixed w/(c+p) ratio. However, the use of the largest possible coarse aggregate may be an important consideration in terms of optimizing modulus of elasticity, creep, and drying shrinkage of the concrete.
ACI 318 recommends that the maximum aggregate size not exceed one-fifth of the narrowest dimension between the sides of the forms, one-third of the depth of slabs, nor three-quarters of the minimum clear spacing between individual reinforcing bars or pre-stressing tendons. Particularly for a high-strength concrete, a coarse aggregate should be chosen that is sufficiently hard, clean, and free of surface coatings.
Fineness Modulus of Fine Aggregates for High-Strength Concrete
If a fineness modulus less than 2.5 is used, the resultant mixture may be "sticky", resulting in poor workability and a higher water demand. In general, because of the increased cement (fines) content of a high-strength mixture, the volume of sand is kept to the minimum necessary to achieve workability and compatibility.
Pozzolan Addition in High Strength Concrete
A Pozzolan Is Defined as a siliceous and aluminous material which in itself possesses little or no cementitious value but in concrete its give strength in two ways, physically and chemically. Physically its finely divided particles fills pores and chemically it react with calcium hydroxide at ordinary temperatures to form compounds possessing cementitious properties.
Generally, a first trial mixture using only cement (no pozzolans) should be prepared and evaluated. So that we could compare strength of high strength concrete with conventional concrete.
Moisture Conditions of Aggregate
The moisture content and aggregate absorption values are used in adjusting the amounts (mass) of aggregates and water to be included in batch proportions. The measured moisture content is used to adjust the mass of aggregate to achieve the necessary mass of saturated surface dry (SSD) aggregates. Absorbed water doesn't become part of the mixing water, so the mass of water is adjusted based on the difference between the moisture contents and absorption of the coarse and fine aggregates, weighted by their dry masses in the mixture.
Testing Age
Because high-strength concrete can gain considerable strength after the normally specified 28-day curing age, many specifications utilize testing ages of 56 or 91 days. This guide attempts to adjust mixture proportions to produce the desired strength at the specified testing age.